Organic dust is common in food production and ignites easily
Organic dust materials such as sugar, grain, spices, potato flour, wood, and similar products, can pose a risk of causing a fatal explosion if they are not properly managed. Operators must have an awareness of the risk of an explosion and require management of the equipment and the production process. Metal dust is no exception. The type of dust and the humidity in which it is stored are crucial.
Many food processing plants also produce significant amounts of dust, such as flavorings and starches, which are often stored in bags and containers with low humidity. Moist products such as fresh fruit and meat, however, can produce huge clouds of dust when they are handled. The moisture in these products makes them much less combustible. Tobacco powder contains a high amount of moisture, which makes it much safer than gunpowder or other dry, flammable materials. It is therefore considered to be a relatively safe dust material.
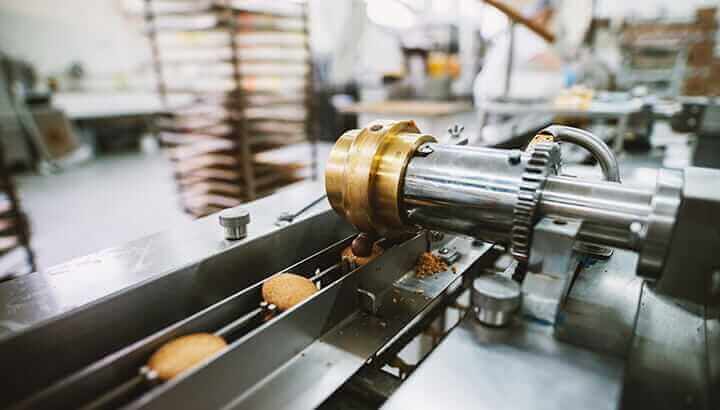
The finer the dust, the higher the risk of combustion
However, the manufacturing and packaging processes produce a certain degree of dust, and the moisture content of the tobacco powder can be reduced to a much drier substance by grinding it. Substantial amounts of dust can be produced when the powder is ground and the particles are blown out into the open air. In addition, the particles can be sucked into the dust collection system ducts at high speed, where they are filtered by a Veil filter made of rubber and then discharged into a bin. The filter is cleaned every hour to prevent spillage of dust. The high-pressure dust is blown through the filter at a very high speed.
Static electricity can build up in the pipe as the dust passes through, and if an excessive amount of dust accumulates in the filter it can cause a serious explosion. A trial was carried out where the tobacco manufacturer’s main product was ground to very fine dust and then sent to a company for analysis. In the company’s test facility, the dust was ignited in order to measure its KST value. The value indicates the maximum rate of pressure rise and is used to estimate the anticipated behavior of the dust, in particular the probability and power of an explosion.
The KST value of the tobacco dust measured was around 70, which is significantly higher than dust generated from wood scraps and rice for example. Nevertheless, it is worth pointing out that flour and sugar have KST values of around 150.
At the conclusion of the risk assessment, the company installed a filter system at the production facility. Although his equipment cannot prevent the dust from exploding, it exhausts the flame and hot air created in such an event, preventing the dust from accumulating and exploding in the tunnel. The dust is then sucked out of the filter and into a vacuum.
Some Key Factors in Combustible Dust Prevention
The vacuum system can then be used to remove excess tobacco powder from the filter. The necessary equipment is in place to prevent these types of dust explosions, which can cause damage to the panels and machinery and cause production downtime of up to 24 hours. Combustible dust is the cause of the greatest danger to personnel. In fact, it is the most common cause of fires and explosions in the workplace. It is also the most difficult to control.
Awareness of the issue is essential, and different companies and industries have different means of dealing with it. Workplace safety assessments should include a number of potential risk factors, including the amounts of dust that are generated and the means by which it is removed. Industrial cleaning routines are an essential aspect of keeping a sanitary environment and reducing the risk of an explosion. The installation of adequate extraction arms, fume hoods, and process ventilation can help to prevent explosions by reducing exposure to man-made fumes and dust, and by ensuring that the dust is removed from the work area. If necessary, install dust particle monitors in every corner of the product site to monitor the level of the dust and get alerts when the dust reaches a dangerous level.
In addition to the appropriate cleaning equipment, the complexity of the production system is also a factor to consider when designing a new plant or production site. The simpler the system, the less damage, reduced maintenance, and fewer errors that can be made during cleaning procedures.